Laminating custom stickers can be a nuanced dilemma and opinions vary widely on the correct answer. Some print processes, like UV screen printed stickers, do not require lamination to be waterproof and outdoors durable. For other printing techniques, such as an HP Indigo digital printer, an unlaminated sticker will not last very long in the outdoor elements.
If the stickers have an outdoor-rated printed process, the decision to laminate can come down to a cost-benefit analysis for the brand. Lamination adds cost to each sticker, but can also provide a really cool look. Some consumers really like the look and feel of a laminated sticker because it feels extra durable.
Let’s learn a little bit more about the pros and cons of laminating stickers.
What are branding stickers?
Branding stickers are stickers that are used for promotional or marketing purposes. They often feature a company’s logo, branding elements, or other identifying information, and are used to create brand awareness and visibility. Branding stickers can be used in a variety of ways, such as being included in the packaging for products, placed on promotional materials or business cards, or used as part of a marketing campaign. They can be made in a variety of sizes, shapes, and styles, and can be used to promote businesses of all sizes and industries.
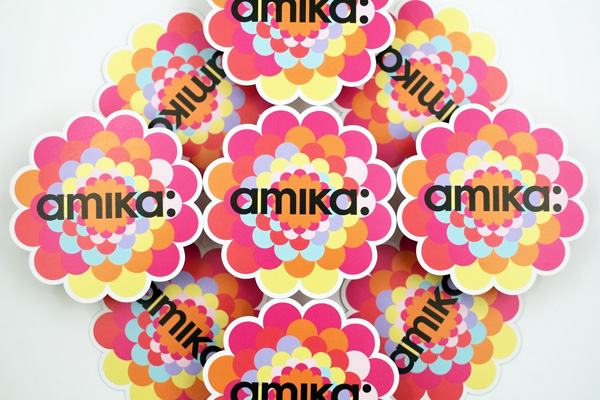
What is the purpose of laminating stickers?
Laminating stickers can serve a number of purposes. Some of the main benefits of laminating stickers include:
- Protection: Lamination can help protect stickers from fading, smudging, and wear and tear. This is particularly useful if the stickers will be exposed to the elements or handled frequently.
- Durability: Laminating stickers can make them more durable and longer-lasting.
- Appearance: Lamination can give stickers a professional, finished look, and can also help to enhance their colors and make them more vibrant.
- Versatility: Laminated stickers can be used in a wide range of environments and applications, as they are resistant to fading and wear and tear.
Overall, the purpose of laminating stickers is to improve their durability, appearance, and versatility, and to protect them from the elements and wear and tear.
Which Print Processes Don’t Require Lamination?
The printing processes that best withstand the sun, rain, wind, and dishwasher are the ones that put the thickness deposit of ink on the material. In this case, screen printing puts down the most durable layer of ink. Screen printing with UV inks is a quick-drying and environmentally-friendly approach to printing outdoor stickers. The average screen print will last 3-5 years in direct sunlight without any noticeable fading of color.
Can Screen Printed Stickers Benefit from Lamination?
Laminating screen printed stickers is a good way to change up the final finish of the decal. Applying a matte laminate will make the print more reader friendly, but less eye-catching. Using a high-gloss laminate is a great way to capture attention. The high-gloss look can be distracting to the eye though.
Laminates can bring out the rich colors of the printed stickers. Some consumers like the look and feel of the laminate because the sticker feels more durable and sturdy. The perceived increased quality can offset the increased cost of adding a laminate.
Laminates are also a good way to protect a screen printed product from heavy abrasion. For instance, a sticker going on the back of a phone case could really benefit from lamination because it will be constantly rubbed against items in a pocket or purse. The initial wear and tear will not affect the print, but over time, the print will have scratches.
What are the most common laminates?
Laminates come in all different constructions and finishes. Here’s a list of the most common types of sticker laminates.
- Matte vinyl laminate
- Gloss vinyl laminate
- Gloss polyester laminate
- Floor graphic laminate
- Pebbled surface laminate
- BOPP selfwound laminate for roll labels.
Are there any cons to laminated stickers?
There are two primary cons to laminating stickers. The first is the extra cost of the laminate. The second con is the added environmental waste that results from unnecessary plastic material.
What is Comgraphx’s Position on Laminates?
We want whatever is best for the customer! We are ambivalent as long as the customer receives the product they want. Most of the products available for sale through our website, such as die cut stickers and custom sticker sheets, are laminated with a matte or gloss laminate. We think these products look really cool with a laminate.